The Turbine Control and Monitor is finished. On the left is the outside showing the Brake Switch, AC Volts, DC Amps, DC Volts and LCD from the Arduino Monitor. The wind speed at the time was about 4 m/sec (8 knots) Inside the unit the LDR 48-30 controller is in the middle with the PSU for the Arduino and the Arduino 'Stack' bottom right. The rectifiers are just out of shot on the far left of the pictures fixed to a big heat sink.
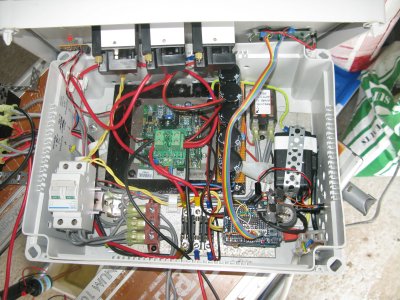
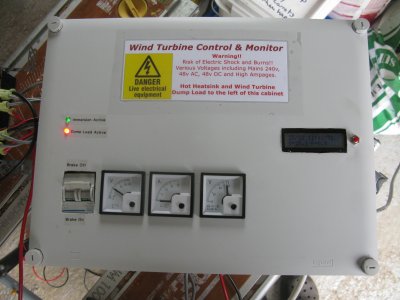